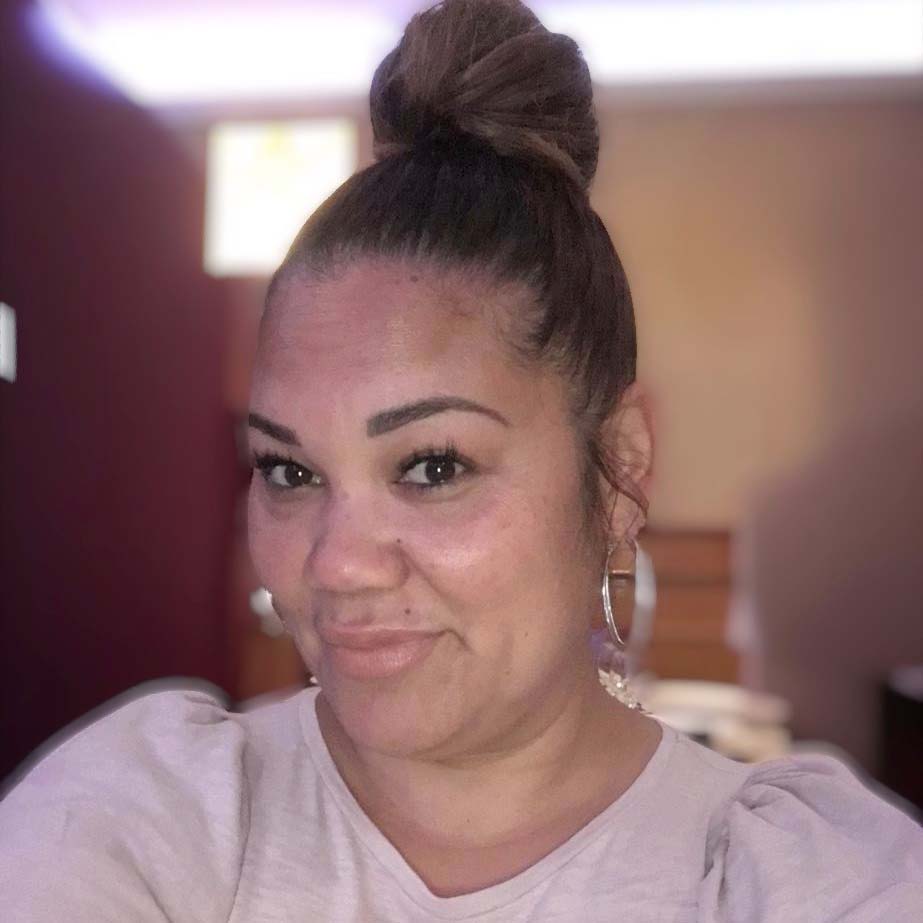
MSCJ provides new opportunities for Jennifer Jeffra
Jennifer Jeffra wanted to expand her horizons after serving in law enforcement for more than 20 years.
August 05, 2024
“I didn't honestly expect to get it, but I knew if I did, I would be beyond excited to take it,” the Trine University mechanical engineering and electrical engineering major said.
Garrett, who is from Greenfield, Indiana, is working this summer in MIT’s Mechanosynthesis Group, which aims to advance manufacturing and its interaction with sustainable growth.
The group focuses on areas such as additive manufacturing, more commonly known as 3D printing; carbon nanomaterials; roll-to-roll processing; printed electronics; and resource-efficient sensing and diagnostic devices.
MIT connections
Garrett learned about the REU through his faculty advisor at Trine, who also sent a recommendation and Garrett’s resume to his own Ph.D. advisors.
One of those was John Hart, Ph.D., who heads the Mechanosynthesis Group. Dr. Hart talked with Garrett about working in his machine design/metal 3D printing lab. An interview with the Ph.D. student Garrett is now working with followed.
He arrived at MIT on May 6 and will continue through Aug. 16.
“Before starting I was able to walk around a bit and look at all the labs,” he said. “The idea of being around all the creative and groundbreaking research taking place at MIT was and continues to be very inspiring!”
The research Garrett is assisting with focuses on new spreading techniques for metal additive manufacturing.
“I am working with one Ph.D. student on two projects: one where we spread fine metal powder (0-20 micrometers in diameter) in thinner layers (50 micrometers thick) than has previously been accomplished and measure the packing fraction (a ratio of how much of the build volume has metal powder versus air),” he said. “Our second project is spreading a similar fine metal powder (0-25 micrometers in diameter) and melting it in thicker layers.”
The end goal, Garrett said, is to develop methods that require less time and power to produce metal 3D prints, while resulting in a smoother surface.
“The surface roughness of a 3D-printed part is a direct result of the diameter of particle used,” he said.
Garrett’s responsibilities have included redesigning the spreading machine for a new spreading direction, experimentation, and troubleshooting the laser printer and spreading rig.
He said he has been able to apply knowledge from courses he’s taken at Trine, including Solid Mechanics, Statics, Dynamics, Systems and Controls, Circuit Analysis, Thermodynamics, Engineering Materials, Introduction to Matlab and Excel, and Physics I and II.
“I have enjoyed seeing the thought process behind tackling each problem,” he said. “I am very interested in going into research when I graduate, so this has been a fantastic first full-time research opportunity.”
“I'm trying to maximize my undergraduate experiences to allow me to go into research with a fuller view on what I'm most interested in.”